Falling Film Evaporator Tube Cleaning
- Posted on
- By David Bokov
- 0
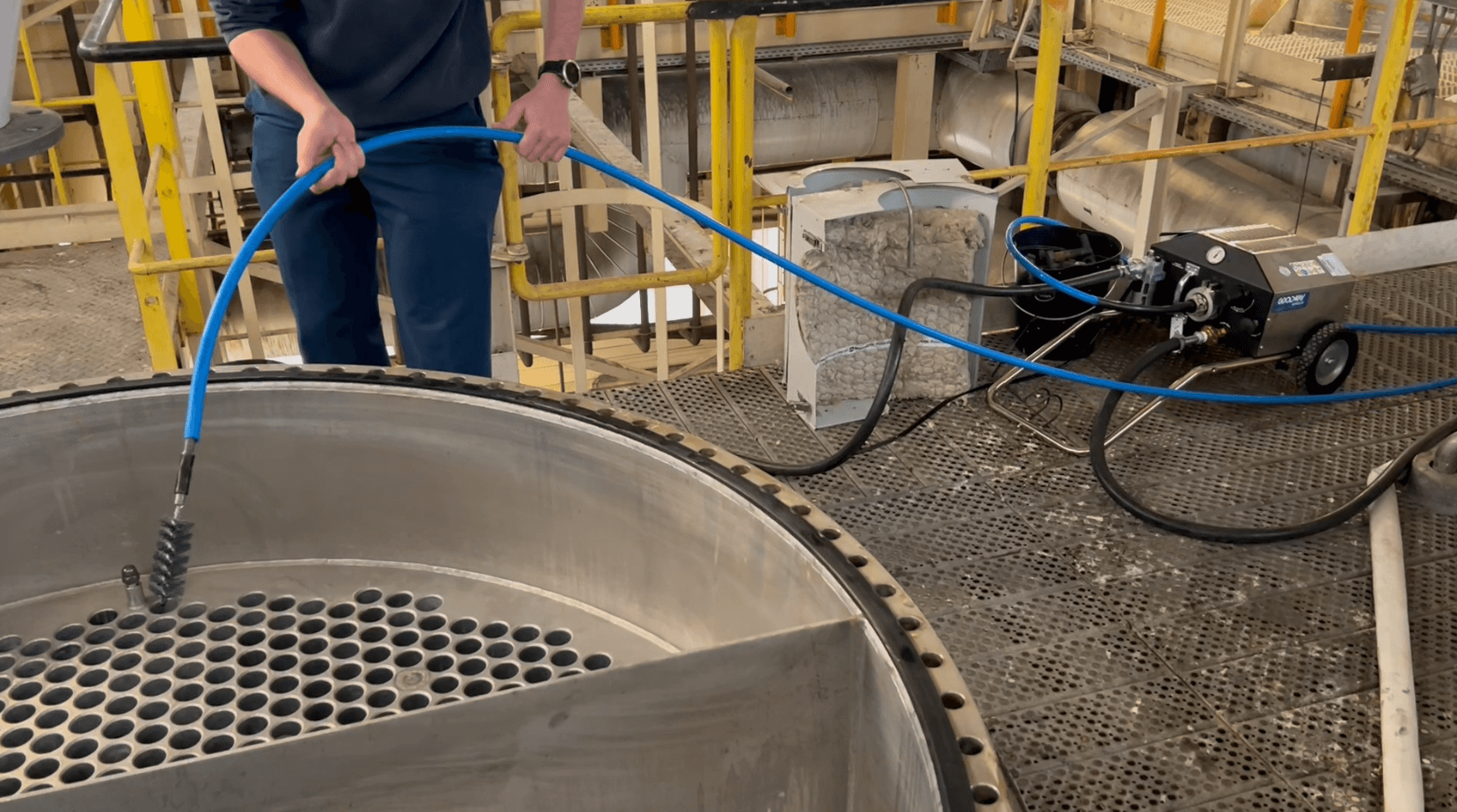
Mechanical tube cleaning of falling film evaporators is an effective technique to remove fouling and possible blockages within tubes. You can read more about this technique in this blog.
Mechanical Tube Cleaning
Falling film evaporators are used in the food industry and in particular at factories active in the dairy industry. These installations have a relatively large number of tubes that will become fouled with the product that flows through them. Over time, especially with dairy products, these deposits can form into a very hard substance, sometimes resulting in blocked tubes. Almost every installation has a standard CIP cleaning, unfortunately fouling can still occur in the tubes. Mechanical cleaning with rotating brushes/tools offers an effective solution.
Fouling in tubes
Falling film evaporators have tubes through which a product flows, depending on the production process this can be different. Over time, particles of the product may stick to the tube wall, despite standard CIP cleaning. After enough time, more deposits will have accumulated, which can lead to various problems. The most common problems due to fouling are:
- Reduced efficiency: because the surface of the tubes is fouled, it becomes more difficult to process the product. This reduces the efficiency of the heat exchanger.
- Reduced production: because the tubes with deposits slowly start to close up, the flow of product through the tubes will decrease. In the case of completely clogged tubes, production drops even further.
- Extreme fouling: in the case of dairy products, it is essential to clean in time. When cleaning is continuously postponed, deposits can build up layer by layer. Eventually forming into a very hard substance, which can only be removed with the most aggressive tools.
Applications and usage of falling film evaporators
A mechanical tube cleaning with rotating brushes/tools is usually used to clean falling film evaporators. These are installations that come in many different sizes and variations. This technique is effective for light, medium, and very hard types of deposits. The brushes and/or tools are recommended based on the hardness and substance of the deposits. This technique can be used to clean tubes with internal diameters between 25-90 millimetres. The technology can be used:
- For falling film evaporators
- For tube lengths from 1 to 12 metres
- For tube internal diameters between 25-90 millimeters
- For light, medium and very hard types of deposits
The cleaning technique
Tube cleaning with brushes is a relatively simple technique. The cleaning always consists of 3 parts: (1) tube cleaning machine, (2) flexible shaft, (3) cleaning brush or tool. The tube cleaning machine is powered by electricity or compressed air and then powers the flexible shaft. This will cause the cleaning brush or tool to rotate in the tube. A small amount of water is added to flush the loosened deposits out of the tubes. Because the rotating brush or tool rotates at high speed, friction is created in the tube. This friction causes deposits which have adhered to the tube wall to come loose.
Every falling film evaporator is different, which is why different variants of products and accessories are available. So it is important to know; how many tubes need to be cleaned, what the internal diameter of the tubes is, what the length of the tubes is, and what kind of fouling is in them. Based on this information, a cleaning package can be recommended.
Different brushes and tools
Various brushes and tools are available for cleaning falling film evaporator tubes. Based on the hardness and substance of the fouling, the correct brush/tool must be selected. The advice is to clean (preventively) as early as possible, when the deposit is still relatively soft. In the case of preventive cleaning, the nylon abrasive brushes will suffice. Because the material is nylon, there will be no risk of damaging the tubes. In the case of (extreme) deposits, where hard scrapers/tools have to be used, there is always a risk of, for example, light scratch formation in the tubes.
- Nylon abrasive brushes: these brushes are used oversized and are made of a type of nylon that has an abrasive effect. This makes it very effective against light and medium types of deposits. The brushes also give a polishing effect, making the tube even cleaner. In case of heavy deposits, these brushes can be used after the scrapers/tools to get the tubes as clean as possible.
- Flex hub centrifugal scrapers: these scrapers are very effective against medium and hard deposits, it is also possible to remove blockages in tubes with these tools. The flex hubs have 3 blades that adjust themselves to the tube internal diameter based on centrifugal forces.
- Drilling tools: these tools are used to open clogged tubes. The cleaning effect is similar to the flex hub scrapers. These drilling tools have stainless steel blades in the middle that ensure that the drill head remains centered in the tube.
- Flare brushes: flare brushes have multiple wires with cobalt balls that adjust themselves to the tube internal diameter based on centrifugal forces. These tools are effective for medium to hard deposits and have a long lifetime due to their construction.
Note: all tools (except the nylon brushes) are made of steel. There is always a risk of (slight) scratching in the tubes, as these are still heavy cleaning tools that rotate at high speed in the tubes. However, these tools are often used in the (food) industry because there is hardly any other effective solution to remove hard fouling and to open clogged tubes. The alternative is to weld the tube closed, which is often not an option.
Features of this technique
Mechanical tube cleaning has a number of features and advantages over other cleaning techniques. You can find these features below.
- Easy to operate: the technique and equipment is easy-to-use. Even with minimal training, it is possible to effectively and quickly clean the tubes of a heat exchanger. This is often an advantage for companies that want to clean their own systems themselves.
- Multiple applications: the tube cleaning system can also be used for other cleaning applications, such as: shell and tube heat exchangers. In that case, you probably only need another set of accessories. This way you can use one device for multiple applications.
- Interesting from a price point of view: the initial investment in a complete tube cleaning package is affordable when compared to other techniques or outsourcing cleaning activities. A tube cleaning machine will last for years, provided it is properly maintained. For future cleanings, it is only necessary to (occasionally) order a new flexible shaft and/or brushes. As a result, the total cleaning costs per system are very low.
- Safe cleaning: the technology is based entirely on the principle of low pressure. This means that no dangerous high pressure is needed for the cleaning process. The only moving part is the brush or tool and it is in the tube for almost the entire time. The safety for both the operator and the installation being cleaned is therefore very high.
- Low water consumption: the tube cleaning machines use approx. 7,5 liters of water per minute to flush away the loosened deposits and to cool the shaft core and brushes. Compared to traditional cleaning techniques, the water consumption of rotary tube cleaning is very low.
Tube cleaners and packages
Falling film evaporators come in many different shapes and sizes. For this reason, Goodway Benelux offers different types of tube cleaning machines and accessories. In addition, there are also complete packages, developed to offer a total solution and to show exactly what is needed in terms of products and accessories. In most cases, the experts at Goodway Benelux recommend a cleaning package based on the application. Please contact customer service for this.
Comments
Be the first to comment...