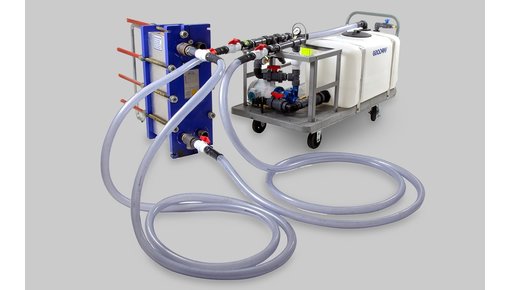
Chemical Cleaning
Heat exchanger cleaning and descaling
Goodway Benelux supplies descaling pump systems and industrial descaler to remove fouling in plate and tube heat exchangers. Industrial strength limescale removers are very effective in removing hard deposits on heat exchange surfaces, such as tubes or plates. Over time, almost all heat exchangers will have to receive some kind of cleaning to restore efficiency levels. Fouling build-up will decrease heat transfer between the two media and therefore lower efficiency. In that case, chemical cleaning of heat exchangers can be an effective solution.
Cleaning in place heat exchangers
When heat exchangers have to be cleaned, it's possible to choose from different cleaning methods. A chemical cleaning is usually performed through the CIP (cleaning-in-place) technique. When cleaning in place a heat exchanger, a descaling pump system is connected to the heat exchanger, essentially creating a closed loop. After that, an industrial descaler, such as Scalebreak-MP, is added to the system and circulated for a few hours. This is also known as flushing a heat exchanger.
The industrial descaler (Scalebreak-MP) removes limescale, rust, and biological deposits from the heat exchanger tubes or plates. When the descaler comes in touch with limescale, it turns it into a liquid suspension which is then flushed out of the heat exchanger. During the cleaning, it may be necessary to add more descaler product if the deposit build-up is higher than expected. Some of the advantages of heat exchanger chemical cleaning in place are listed below:
- Heat exchanger can be cleaned on site, it is not necessary to clean it off site.
- Very little disassembly required, which keeps the cleaning downtime as short as possible.
- With plate heat exchangers it is not necessary to take the plates apart. This saves a lot of time and costs, because the gaskets do not have to be replaced. In addition, there is less chance of leakage by reassembling the plates incorrectly.
- A preventive CIP program ensures optimum efficiency and lifespan of the installation.
Descaling pump systems
Goodway Benelux supplies several different descaling pump systems to actually circulate a descaler agent through the heat exchanger. Based on various information, such as the volume, the correct descaling pump system should be selected. Below you can find the 3 pump systems.
- GDS-C40: mobile descaling pump system for circulating volumes up to 250 liters. It has a flow rate of 56,7 liters/minute. Ideal for cleaning-in-place smaller plate and tube heat exchangers.
- GDS-C92: mobile descaling pump system for circulating volumes up to 400 liters. It has a flow rate of 79,5 liters/minute. Ideal for cleaning-in-place small to medium plate and tube heat exchangers.
- GDS-100: mobile descaling pump system for circulating volumes up to 3600 liters. It has a flow rate of 360 liters/minute. Ideal for cleaning-in-place medium to large plate and tube heat exchangers.
Industrial descaler - Scalebreak-MP
Goodway Benelux mostly supplies Scalebreak-MP for heat exchanger descaling, which is an industrial descaler developed to clean technical installations, such as heat exchangers. The descaling chemical has a unique formula that allows it to be used on almost any material without causing damage. In addition, Scalebreak-MP is biodegradable and (due to the formula) is exempted for the transport of hazardous substances. Common deposits in heat exchangers, such as: limescale, rust, and biological deposits can be easily removed by circulating Scalebreak-MP.
Increase heat exchanger performance
Shell and tube heat exchangers have tubes that become fouled over time with deposits such as algae, slime, biological fouling, rust, and scale build-up. A fouled heat exchanger will be less efficient and decrease in output. In addition, the lifespan of the installation and components can be shortened by keeping it in a fouled condition. Descaling the heat exchanger with descaling pump systems and industrial descaler is a very effective way to remove the deposits in a safe and efficient way. Furthermore, due to CIP, almost no disassembly is required to take place, which reduces downtime.